Intro:
The project started at 7 pm one Friday night. On my drive home from work I got a call from a good friend who started excitedly explaining his idea for a longboard skateboard brake. He tells me he wants to sell them next week at his school entrepreneur fair. As a realistic person, the nay-say side of me started jumping up and down but as we talked more I decided this was exactly my type of challenge. We had ten days to take his idea to products that can be sold and used. I got home and immediately started sketching out different concepts on my whiteboard, then designed a few in CAD to see how they might work.
In hindsight, the place to start should’ve been an online patent search to get a feel for what else was out there.
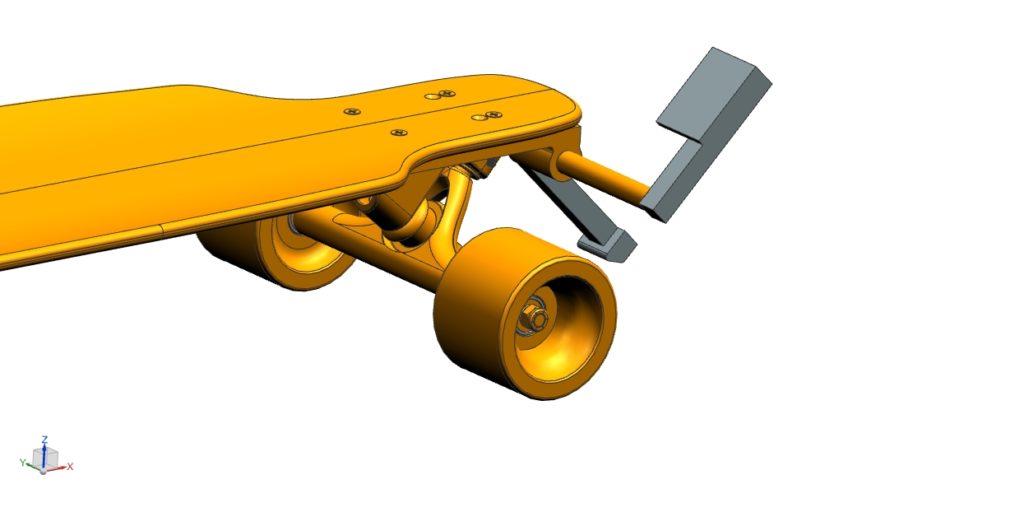
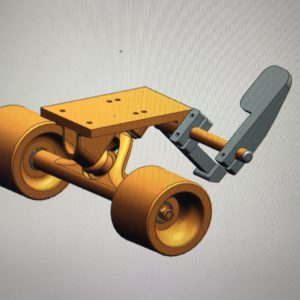
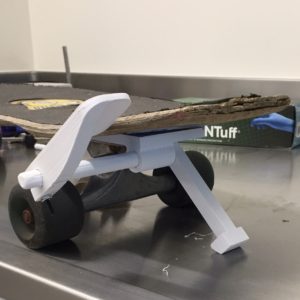
He loved this design and wanted to proceed with it. In an evening I redesigned the brake in a way that could be easily fabricated with common materials on McMasterCarr while still being robust.
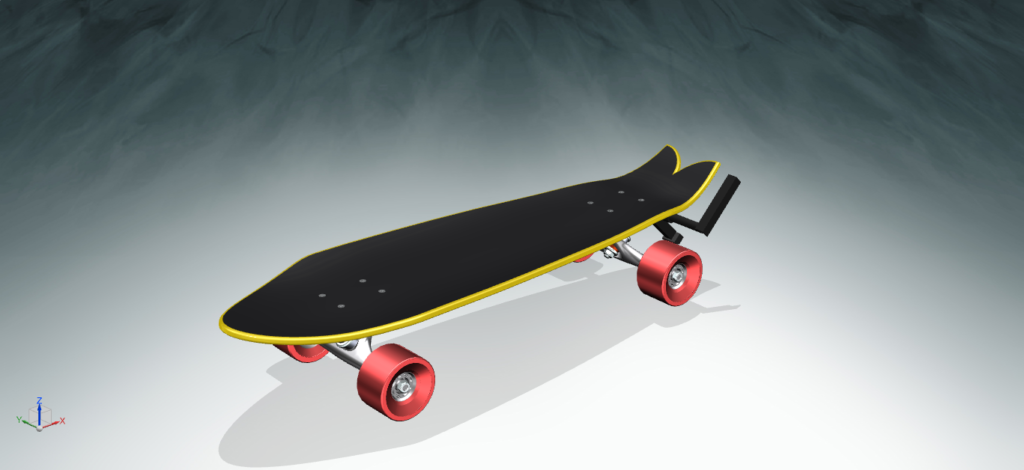
I then built an order on McMasterCarr with enough parts to fabricate ten brakes which I sent him for purchase. I also built a “cut list” and sent his machine shop operator .dxf files for waterjet cutting of the baseplate.
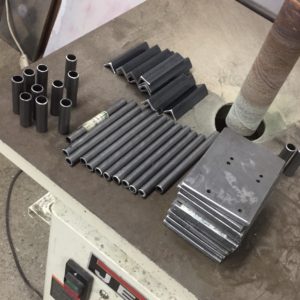
Finally we had the parts welded together (Luckily his Aunt is an artistic welder) and painted with Rustoleum Bedliner Spray.
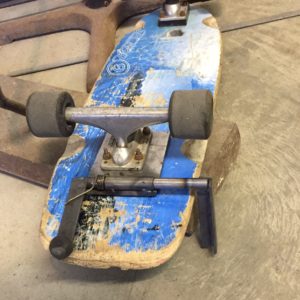
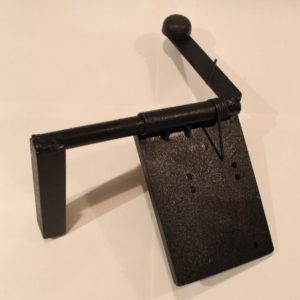
Lessons Learned:
In total I spent about 25 hours on it and cost of parts was just under $200. I never liked the idea of using brake pads made of rubber or similar because as the pad wears, tiny bits of rubber enter the environment and will inevitably end up in the ocean. We found the the rubber brake pad was too soft anyways and are using pads made for roller blades currently. I want to look into materials that are naturally found in the environment such as wood, limestone or clay.